What is Veneer?
Timber veneer sheets are made from a natural and renewable resource, unlike their non-renewable counterparts, such as steel, aluminium and plastic sheets. Because they are thin yet strong, timber veneer panels cover approximately forty times more space that solid timber. Therefore, they are the most economical way of utilising our precious wood.
Timber veneer panels are produced by slicing or peeling certain logs. They are cut at approximately 0.6mm, which is the normal thickness for the Australian market, or they are peeled at a diverse range of thicknesses.
To create specific grain patterns manufacturers can use several methods.
What Is Fusion Veneer?
When consistency and uniformity of colour, grain and texture are important, Sharp’s collection of fusion veneers provides a stylish answer in our range of exclusive reconstituted timber panels.
Our fusion veneers don’t have knots or other defects like real timber panels, which is why colour matching won’t be an issue. Fusion panels are made from unsuitable timber waste that would normally be chipped and deposited into landfill. The waste is processed to form a square block and then sliced into rectangular panels.
The result is a stunning panel whose surface displays an even pattern and colour. These fusion panels are stable and free from random characteristics and blemishes normally found in natural timber veneers.
At Sharp Panels we are proud to be utilising environmentally responsible techniques to turn wooden veneer waste into something beautiful that still contains the naturalistic of real wood, ages like real wood and feels like real wood. We care for our forests and we strive to produce a stunning product that is also environmentally friendly.
Fusion veneers are ideal to be used for kitchens, furniture, commercial fit outs, wall panels and doors where consistency and quality shared with the warmth of timber is essential.
Should you have any further questions regarding our products, please do not hesitate to contact us now. We are always happy to assist our clients find the ideal product to suit their needs and budget.
Patterns
Flat or Crown Cut
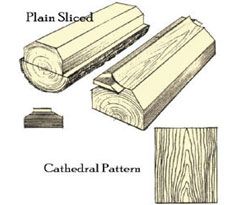
Timber veneer sheets that are cut tangentially to the grain, meaning parallel to the growth rings of the tree, are referred to as “flat cut” or “crown cut” sheets. This cutting methods results in a beautiful pattern of bold sweeping curves and ovals along the centre of the leaf, with striped grain nearer the edges. The design is called cathedral pattern.
Quarter Cut
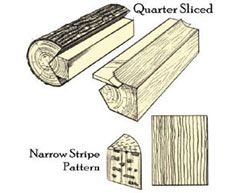
This cut is characterised by a pattern of relatively straight line grains and is produced by cutting at a right angle to the growth rings.
Rotary Cut
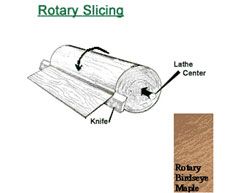
Rotary timber veneer sheets are most commonly produced in thicknesses ranging from 0.9mm up to 3mm and are predominantly used in plywood. It is created by peeling the timber from the log in a continuous ribbon using a lathe blade that operates at high speed. The resulting pattern is a bold, multi-coloured or non-descript swirl grain.
The following diagram shows the individual parts of the tree, where the different types of timber veneer panels are cut from.
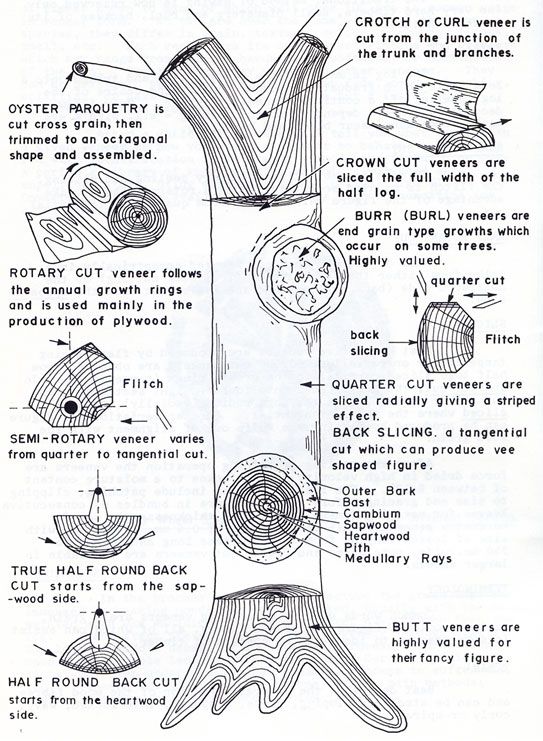
Methods of Assembling Veneer Leaves
Various visual effects can be achieved by different methods of joining. Below you can find an overview of the most commonly used ones.
Book Matching
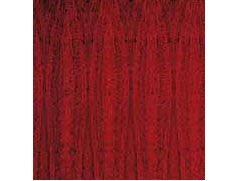
This is the most widely used methods of joining, in which each veneer leaf is a mirror image of the next one. This distinct look is created by alternatively folding leaves out, as if opening the centre spread of a book.
Slip Matching
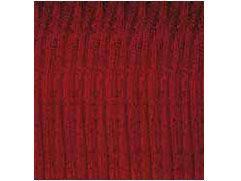
When slip matching, the veneer leaves are laid face up, side by side. The result is a pattern in which the same grain pattern is being repeated at the width of each leaf across the layon.
Mismatched or Random Matched
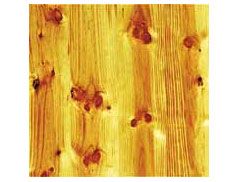
For this method individual leaves are randomly matched to create a specific effect. Knotty Radiata pine is commonly laid this way. This method allows characteristics such as clusters of knots to be dispersed more evenly across the timber veneer sheets.
Reverse Slip Matching
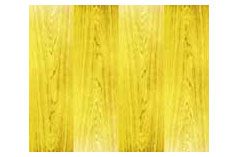
First the leaves are slip matched, then every second veneer leaf is turned end for end. This allows manufacturers to “balance” crowns in the leaves, to ensure not all crowns appear at one single end only.